Metals
Indium Metal
Indium is an extremely versatile metal that lends itself to a wide variety of technical applications, combining a low melting point with high thermal conductivity. When converted into indium oxide, it is the starting point for transparent conductive oxide materials such as indium tin oxide (ITO).
Powered by Indium Corporation
- Various Shapes, Sizes, and Forms
- Purity Levels From 3N to 6N and Up
- Ready for Prototype or Mass Manufacturing
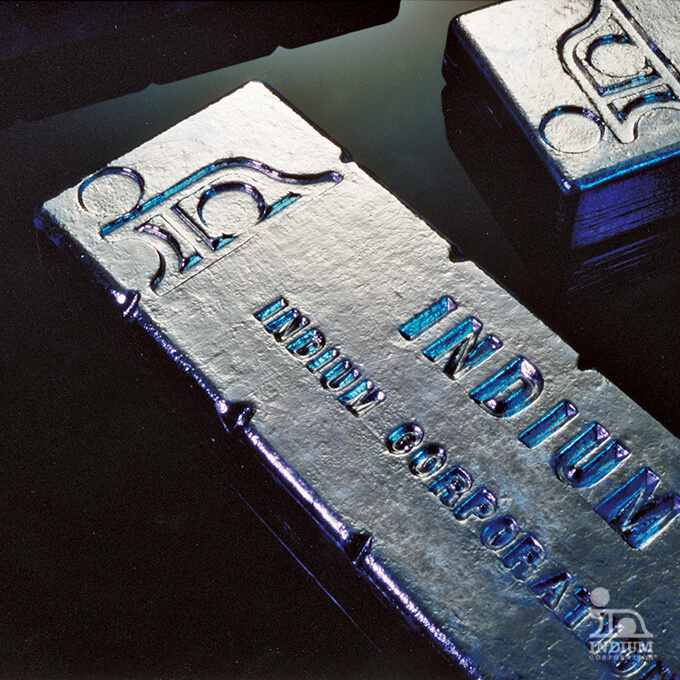
Product Overview
Various Shapes
The standard indium metal product is provided in the shape of prismatic ingots, but numerous sizes and form factors are available. This includes custom designs to match the specific dimensions needed for electroplating tanks, along with shot sizes ideal for evaporation applications.
Special Forms
Indium metal is available in thin sheet foil and wire forms. Indium Corporation also offers a wide range of custom preforms to meet specific build requirements.
Purity
Indium metal ingots represent the core supply of this versatile element, encompassing a wide range of impurities across our product categories. The predominant purity level for indium metal typically stands at 4N (99.99%). Higher purity levels are also offered.
Thermal Interface Materials
Indium is a preferred thermal interface material (TIM) due to its excellent thermal conductivity and ability to form a strong, flexible bond between connected components.
Related Applications
Indium metal is suitable for a variety of applications.
Related Markets
Indium is widely utilized across markets for a multitude of applications.
Expert Support for Reliable Results
Do you have technical questions or sales inquiries? Our dedicated team is here to help. “From One Engineer to Another®” isn’t just our motto—it’s our commitment to delivering exceptional service. We’re ready when you are. Let’s connect!
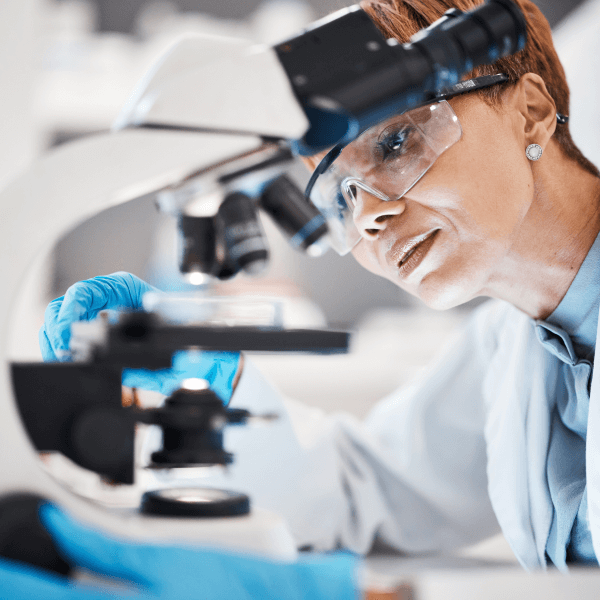
Looking for Safety Data Sheets?
Access everything you need — from technical specifications to application guidance — in one convenient location.
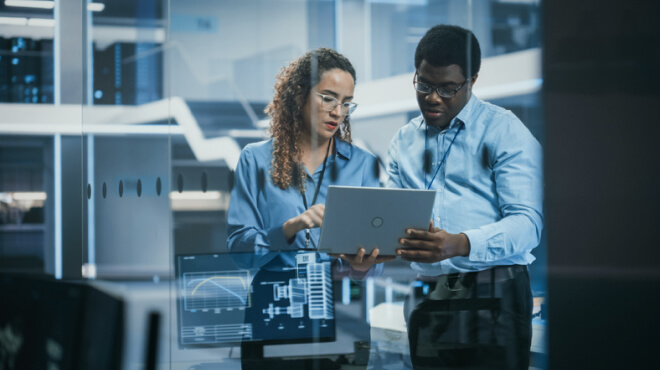
Your Success
is Our Goal
Optimize your processes with the latest materials, technology, and expert application support. It all starts by connecting with our team.